Where Water Turns to Wonder: The Charm of River Watermills
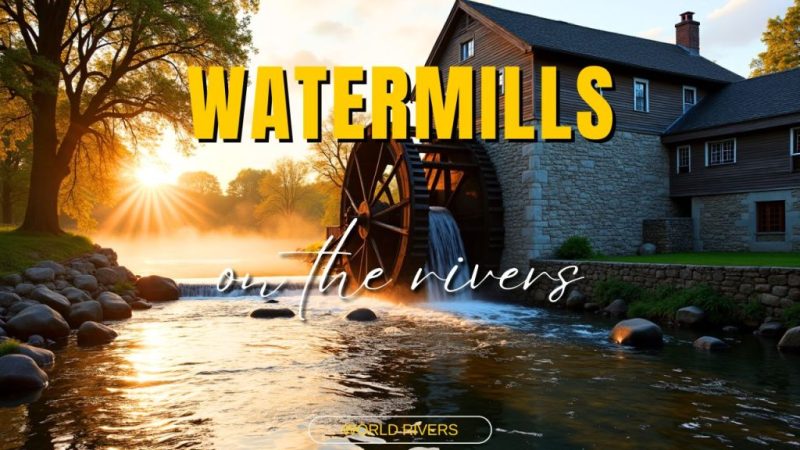
Whispers of water and wood—discover how rivers once powered the world through the timeless charm and quiet genius of old watermills.
There’s something undeniably magical about a watermill. Maybe it’s the steady turning of the wheel, the rhythmic splash of water as it meets wood and iron, or the way these quiet machines seem to belong to another time — a time when rivers didn’t just inspire poetry, but powered civilization itself.
Long before electricity hummed through wires and cities pulsed with digital life, rivers were the engines of human progress. And watermills, perched along their banks, were among the first tools that helped people transform natural energy into something useful. They ground grain into flour, pulped rags into paper, crushed olives into oil, and even hammered metal — all powered by the simple force of flowing water.
The concept is beautifully simple: as the river flows, it turns a wheel. That wheel connects to a system of gears and shafts, translating the wheel’s rotation into motion. Depending on the design, the mill could be vertical or horizontal, undershot (with the water flowing beneath the wheel) or overshot (with water cascading from above). And from that elegant motion, an entire village could eat, work, or trade.
Watermills started in ancient Mesopotamia and reached their peak in mediaeval England. By 1300, more than 10,000 watermills altered the English landscape. Their design showed remarkable resilience through time. Water turbines in the 19th century achieved efficiency rates above 75%, laying the groundwork for modern hydroelectric power.
This piece takes you through the remarkable story of watermills. You’ll find details about their ancient origins, technological development, and their effects on industrial growth. The text shows how these machines operated, their many uses, and their vital role in building riverside communities through the centuries.
The Ancient Origins of Watermill Technology
People started to make use of water power thousands of years ago when early civilizations looked for ways to reduce manual labour in daily tasks. Archaeological findings show that water-powered devices evolved step by step in different regions. This technology evolved into sophisticated watermills that reshaped human productivity for thousands of years.
A Brief History of Watermills Around the World
The story of the watermill spans continents and civilizations, tracing the ingenuity of early societies as they harnessed the elemental force of water to ease human labor.
The horizontal watermill emerged first in the Near East, showcasing a remarkably simple yet effective mechanism: a horizontal water wheel directly connected to the grinding shaft via a vertical spindle. Suited to swift-moving but shallow rivers, these mills rotated slowly—around 15 to 20 revolutions per minute—but steadily, ideal for consistent grain grinding.
In ancient China, during the Han dynasty (206 BC–220 AD), the watermill flourished alongside other brilliant inventions like the chain pump. These early Chinese mills played a critical role in agriculture, particularly in the irrigation of rice paddies, and marked one of the earliest integrations of waterpower into everyday life.
Meanwhile, in Persia (modern Iran), watermills were powered not just by rivers, but also by ingenious use of qanats—underground channels tapping into spring water. Persian mills often featured funnel-shaped towers, narrowing the water flow from a 5 to 6 meter height difference to concentrate energy before driving the mill. Sophisticated mechanisms, such as internal weirs and diversion channels, allowed precise control over the milling process.
In the Indian subcontinent, water technology dates back millennia, to the Harappan civilization (ca. 3000–1500 BC) and the Vedic period. By the 4th century AD, flour mills known as “Gharats” became widespread. These small-scale mills lined mountain streams, using kinetic water energy to turn wooden shafts and grind flour. During the Indus Valley period, waterpower was also used for irrigation and lifting water.
The Islamic world inherited and transformed earlier Greco-Roman technologies, beginning in the 7th century. Drawing upon the Byzantine legacy, Muslim engineers innovated upon both horizontal and vertical watermills, expanding their applications across the empire. By the 11th century, watermills—ranging from gristmills and sawmills to steel and sugar mills—proliferated from North Africa and Al-Andalus to Central Asia and the Middle East. Notably, Muslim inventors pioneered water turbines, crankshafts, and advanced gear systems. Some even tapped the energy of dams to boost power output, laying foundations for future hydraulic engineering.
From the slow-turning millstones of ancient Asia to the complex, gear-driven mechanisms of medieval Islamic lands, watermills reveal a shared legacy of human innovation—channeling nature’s flow to nourish, grind, and grow civilizations.
Early water-powered mechanisms in Mesopotamia
Mesopotamian civilizations led the way in creating some of the first water management systems, which laid the groundwork for later mechanical breakthroughs. Settlements like Kish, Lagash, Ur, Umma, and Uruk built advanced irrigation networks in the fertile lands between the Tigris and Euphrates rivers to channel water to crops. These communities faced major hurdles. Melting ice from Anatolia raised water levels during warm seasons and brought heavy silt that built up in the poorly drained riverbeds.
Mesopotamians created artificial irrigation techniques to deal with unreliable water sources. They developed the earliest known version of the water wheel by the mid-4th century BC. This horizontal, propeller-like device ground flour. The technology proved so effective that it spread to southern Europe and China.
State involvement in Mesopotamia’s water management changed over time. Instead of maintaining steady centralised control, government intervention in irrigation systems matched how ruling institutions used agricultural land.
Greek and Roman engineering innovations
Greeks perfected two vital parts of watermill technology: the waterwheel and toothed gearing systems. The Greek engineer Philo of Byzantium (ca. 280−220 BC) wrote the earliest known description of water-driven wheels in his technical treatises Pneumatica and Parasceuastica.
Historical research shows that the horizontal-wheeled mill came from the Greek colony of Byzantium in the first half of the 3rd century BC. The more advanced vertical-wheeled mill appeared in Ptolemaic Alexandria around 240 BC. Greek water mills worked through simple yet effective mechanical principles. They used either undershot waterwheels powered by flowing water beneath or overshot designs that channelled water from above.
Romans improved and spread watermill technology throughout their empire. Vitruvius wrote the first detailed technical description of a watermill around 40/10 BC. His design featured an undershot wheel that transmitted power through an advanced gearing mechanism. Archaeological evidence shows that Roman watermill technology made its breakthrough in the 1st century AD, not during the Middle Ages as many once thought.
The first documented watermills
The first clearly documented watermill appears in the writings of Greek geographer Strabo. He described a water-powered grain mill at King Mithradates VI’s palace in Cabeira, Asia Minor, before 71 BC. This mill, called an ydraletas, marked a key moment in recorded watermill history.
Roman engineering advanced watermill technology faster for industrial uses. Roman encyclopaedist Pliny mentioned water-powered trip hammers operating throughout Italy by 70 AD. Evidence of a fulling mill from 73/74 AD has been found in Antioch, Roman Syria.
The 2nd century CE Barbegal complex near Arles in southern France stands as the most impressive early industrial site. This remarkable facility had 16 overshot waterwheels arranged in two parallel rows down a hillside. It could produce 25 metric tonnes of flour daily and feed about 27,000 people. Archaeologists call it “the greatest known concentration of mechanical power in the ancient world”.
Romans developed more sophisticated applications by the 3rd century AD. The Hierapolis water-powered stone sawmill became the earliest known machine with a crank and connecting rod mechanism. Recent archaeological discoveries confirm that Romans reached their technological peak in watermill development during the 2nd and 3rd centuries CE. This shows they used mechanical technology much more extensively than previously thought.
How Roman Watermills Revolutionised Ancient Industry
Roman engineers turned basic water-powered tools into groundbreaking industrial systems that created massive concentrations of mechanical power. Their state-of-the-art designs paved the way for large-scale production long before the Industrial Revolution. Recent archaeological findings show they used mechanical technology much more extensively than we once thought.
The Barbegal complex: Rome’s industrial marvel
The Barbegal watermill complex stands as the most impressive example of Roman industrial genius. Built in the 2nd century CE near Arelate (modern Arles) in southern France, this remarkable facility had 16 overshot waterwheels. These wheels were arranged in two parallel rows of eight mills that cascaded down a hillside. Experts consider it “the greatest known concentration of mechanical power in the ancient world” with no equal in Roman or Asian civilizations.
The 120-130 CE old complex showed exceptional production capabilities. Its 16 wheels could run at the same time and produce about 25 metric tonnes of flour each day – enough to feed over 27,000 people. This output was nowhere near what animal or human-powered mills could achieve.
In stark comparison to this, earlier theories linked the complex to Emperor Constantine in the late 3rd century. However, 1990s excavations revealed Barbegal as an early pinnacle of technological advancement. The complex’s location near major ports of Arles and Fossae Marianae suggests ships visiting these harbours might have used its massive flour production for bread.
Spread of watermill technology across the Empire
Archaeological findings show Roman watermill technology took off in the 1st century CE and quickly spread throughout the Empire. More watermill remains exist from the 1st to 4th centuries CE than the early mediaeval period (5th-9th centuries). This suggests Romans used these mills more widely and intensively.
Watermills started out grinding grain. As the technology improved during the 2nd and 3rd centuries CE, Romans adapted it for many industrial uses. Archaeologists have found waterwheels powered mechanical saws to cut timber and stone at Hierapolis and Ephesus. They also discovered evidence that waterpower ran forge hammers for metalworking and helped make textiles in fulling mills.
The connection between watermills and Roman aqueducts became vital for military logistics. Romans built mills near steady water supplies from aqueducts to create reliable food production systems for armies and city dwellers. Their modular design let them quickly set up mills in conquered territories, which supported both military campaigns and new business ventures across the growing Empire.
Medieval Expansion: Watermills Across European Rivers
The collapse of the Roman Empire led to the amazing growth of watermill technology across medieval Europe. These machines became more common and advanced than ever before. People in medieval times didn’t lose this technology during the “Dark Ages.” Instead, communities saw these watermills as a great way to boost their economy.
Domesday Book records: 5,000+ mills in England
William the Conqueror’s Domesday Book from 1085 gives us a fascinating look at England’s watermills. This detailed survey showed about 6,000 working watermills across England. These made up over 99% of all known mills from before the eleventh century ended. A closer look at the numbers shows at least 5,624 watermills existed during this time. The Great Domesday alone listed more than 5,000 of these.
The numbers tell an impressive story – there was roughly one mill for every two settlements in the country. This shows how deeply watermills had become part of mediaeval England’s fabric. Different areas had different patterns of ownership. Some mills belonged to multiple owners. Norfolk stood out with 87 manors having shared mills. Lincoln had 38, Wiltshire 23, and Suffolk 15. This shared ownership might show how communities worked together to make the most of their resources.
The number of watermills grew rapidly after the Domesday survey. Historical records suggest English watermills doubled in the next two hundred years. They reached around 10,000-12,000 by the late 13th century. This growth matched the rising population and a more sophisticated economy.
Monastic orders and watermill development
Monks, especially the Cistercians who started in 1098, pushed watermill technology forward throughout medieval Europe. Under St. Bernard’s guidance, Cistercians saw watermills as their path to financial freedom. Within 50 years of starting, their monasteries became leaders in water power and farming technology.
Cistercian monasteries did things differently than before. They built state-of-the-art hydraulic systems. Their buildings sat on specially made canals that ran through the entire monastery grounds. This clever setup let one water source do many jobs: power mills, provide drinking water, and even clean waste.
These monastic orders found new ways to use watermills beyond just grinding grain. Their creative uses included:
- Woodcutting operations
- Metal forging
- Olive oil production
- Textile processing
- Irrigation systems
Cistercian monasteries became medieval factories that shaped how other communities worked. Their success in controlling water power helped make them wealthy landowners across Europe.
Economic impact on medieval communities
Watermills changed medieval economics completely. These machines were huge investments – among the biggest in pre-industrial Europe. Mill owners became rich and powerful. Feudal lords saw these mills as money-making machines.
The benefits were huge. One miller could do work that used to need many workers. This created new opportunities but also changed traditional work patterns. Lords who built mills charged mandatory fees, which gave them steady income and social control.
Watermills helped create national markets. They made production faster, bigger, and cheaper, which opened new business opportunities. The textile industry changed dramatically when watermill-powered fulling replaced hand labour. This moved production from cities to rural areas near water power.
The scattered political landscape actually helped spread watermills. Studies of river basins show areas with divided authority built more watermills. This supports Marc Bloch’s idea that giving legal rights to lower-ranking elite members helped watermills spread across Europe.
Watermills became crucial infrastructure on European rivers by the end of the medieval period. These amazing machines turned grain into flour, powered industry, and reshaped Europe’s economy.
The Industrial Revolution and Watermill Evolution
Watermills went through dramatic changes during the Industrial Revolution. They moved from medieval technology to sophisticated power systems that drove early manufacturing. Steam power later took over, but these water-driven machines played a significant role in Britain’s industrial growth through innovation and diversification.
Technological improvements in waterwheel design
Scientific research transformed waterwheel efficiency in the 18th century. John Smeaton’s groundbreaking work in the mid-to-late 1700s improved waterwheel performance substantially. His systematic approach to waterwheel design created engineering principles that manufacturers could apply with consistency.
Lester Pelton’s 1880 patent of the Pelton wheel marked a notable breakthrough. His design used an impulse principle that improved efficiency and power output compared to traditional waterwheels. This innovation worked great in mountainous regions with high-pressure water sources.
Wheel designs improved to extract maximum power based on site conditions:
- Overshot wheels (water hitting the top) were 2.5 times more efficient than undershot designs
- Breastshot wheels (water hitting the middle) offered moderate efficiency
- Undershot wheels (water hitting the bottom) were least powerful but simple to construct
These improvements led to highly efficient water wheels by the 19th century. Reaction turbines appeared around 1825, and impulsion turbines for high chutes arrived by 1880. These innovations improved watermill capabilities and set the foundation for hydroelectric applications.
Transition from grain milling to industrial applications
Early watermills focused on grain processing, but their industrial uses expanded rapidly during the 18th and 19th centuries. Richard Arkwright’s water frame, powered by waterwheels, became vital in mechanising textile production. Water-powered trip hammers and blast furnace bellows reshaped metal manufacturing.
Waterpower mechanised manual processes in the textile industry, such as fulling—the cleaning and thickening of cloth. Production moved from urban centres to rural waterways, which deepened these towns’ commitment at cities’ expense.
Watermills powered various industrial activities:
- Sawmills and timber processing
- Metal forging and industrial hammers
- Tanning of hides
- Vegetable oil pressing
- Rock crushing for mining operations
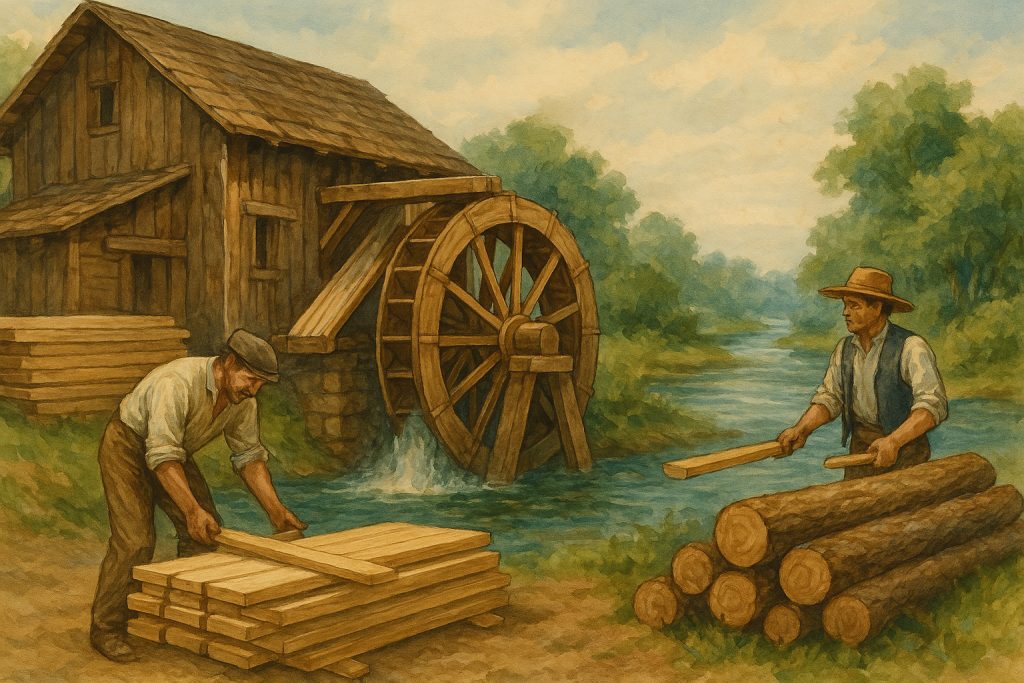
Large industrial settings used a main wheel to generate power. Belts and shafts transferred this power to multiple machines, which enabled complex manufacturing processes in a single facility.
Competition with steam power
Waterpower dominated the early Industrial Revolution, but steam emerged as a strong competitor. Watermills proved resilient—they still produced two-thirds of British grain milling power in 1870.
Different regions adapted to steam at different rates. Greater Manchester’s waterpower resources became limited by 1838. The heart of British cotton production faced challenges from increased factory mechanisation and crowded waterways. A drier 19th-century climate made things worse. Most other British counties and river basins managed to keep abundant waterpower resources.
Steam had key advantages: it worked year-round, whatever the weather conditions, and allowed factories to operate away from rivers. Steam engines often worked alongside watermills in hybrid systems. In stark comparison to this, steam engines helped recirculate water for hydropower-dependent factories late into the 19th century.
Cheap electrical energy ended up making traditional watermills obsolete in developed countries by the early 20th century. Some rural mills continued their commercial operations throughout the century.
Understanding Different Watermill Types on Rivers
Watermill designs changed through history to match different river conditions. Simple horizontal wheels evolved into complex overshot designs. Each type showcased clever engineering that made the most of local water resources.
Horizontal wheel mills: the earliest design
Norse or Greek mills were the first and simplest watermills. These wheels turned around a vertical axle with the upper millstone attached directly to it. This design didn’t need complex gearing. Irish archaeological discoveries revealed expertly crafted horizontal water-wheels from the early medieval period (c. AD 612–1124).
These wheels had a simple hub with wooden paddles arranged in a circle. Water flowing sideways hit these paddles to make them spin. Two main types became popular: wheels with flat vanes (the classic ‘Norse’ style) and ones with curved “scooped” paddles that worked better.
An artist’s rendition of a horizontal wheel mill, brought to life with gentle brushstrokes and rustic charm.
These simple mills showed remarkable technical skill. The Irish examples had precise mathematical spacing between paddle mortises. This was quite a feat given the hub’s small surface area. Mill workers made wheel parts as templates for repairs, which points to standardised production methods.
Undershot wheels for gentle flowing rivers
Greeks and Romans mostly used undershot waterwheels because they were easy to build. These wheels sat directly in fast-flowing rivers with their paddles dipped at the bottom.
Flat areas without natural slopes were perfect for these wheels. They just needed enough water speed to turn the paddles. Their simple design let builders place them in bridge arches or on anchored barges in the middle of streams [88, 89].
These wheels had some big drawbacks. The design worked against itself – as the wheel entered the water behind the main flow and lifted out ahead of it, it slowed itself down. These wheels only captured about 20% of water’s potential energy.
Overshot wheels: maximising power from height
Overshot waterwheels became more popular than undershot designs after the 13th century. A 1928 study showed that well-designed overshot wheels could reach 85% efficiency. This was about 2.5 times better than undershot models.
Overshot wheels fixed the undershot wheel’s problems by getting water from above. Instead of paddles, these wheels had buckets around their edges that filled with water. Full buckets created weight that turned the wheel, then emptied into a spillway below. The wheel’s position above the spillway meant water never slowed its rotation.
These wheels needed specific conditions – usually a water source from above with at least a 15-foot vertical drop. They worked best with height differences between 2.5-6 metres and flow rates under 0.2m³/s per metre width. Building them needed dams and raised head races, but their better efficiency made them perfect for places with less water and moderate falls.
Breastshot and pitchback variations
Two clever designs emerged for situations where neither undershot nor overshot wheels worked well. Breastshot wheels got water at axle height, filling buckets that moved down with the wheel. These wheels excelled with moderate height differences of 1.5-3 metres and higher flow rates of 0.3-0.65m³/s per metre width.
Pitchback wheels (sometimes called backshot) solved a practical issue: overshot wheels turned the opposite way from undershot wheels, which meant rebuilding all mill machinery when switching types. These wheels got water near the top from a pentrough above, but made it flow with the wheel’s rotation, keeping the same direction as undershot wheels.
By the 1800s, these designs had reached impressive technical levels. Modern water wheels built on scientific principles achieved 75-89% efficiency. Breastshot wheels typically hit 75-80% while overshot and pitchback designs reached 85-90%.
How Watermills Work: Mechanics and Power Generation
Watermill mechanics revolve around energy conversion that turns water motion into rotational power for practical work. Water provides steadier energy than wind power, which changes with weather conditions. You can use this energy throughout the year.
Using water’s potential energy
Watermills work on a simple principle: moving or falling water contains energy we can capture. Two main factors determine this potential energy: water flow volume and the height difference (head) of the fall. Water weight in buckets turns overshot wheels, while flowing water strikes against paddles in undershot wheels.
Choosing a watermill’s location needs careful planning because each site comes with its own challenges. Millwrights created channels called mill races to redirect river water. The headrace moves water from the mill pond to the wheel, and the tailrace carries water away after it passes the wheel. Most watermills had millponds that stored water like energy banks for busy
Sluice gates were used to regulate the rush of water that powered the mill wheels, opening and closing with precision to control the force delivered to the machinery.
Gearing systems and power transmission
A watermill’s brilliance shines through its power transmission systems. The wheel’s horizontal shaft connects to a large pit wheel in vertical waterwheels. This wheel meshes with a smaller gear (the wallower) on a vertical shaft to create that vital 90-degree rotation change. The vertical shaft then turns a larger great spur wheel that powers smaller stone nuts attached to the runner stones.
Each gear train step speeds up rotation, which lets millstones spin faster than the water wheel. This mechanical advantage helped even smaller wheels generate enough power for grinding. The gearing ratios determined how many millstones one wheel could power. By the 19th century, a well-designed system powered up to four stones at once.
The millstones—often hewn from durable granite, or any stone available locally. Sometimes, the finest stones came from afar, imported at considerable cost, but prized for their longevity; a well-kept pair could last a century.
Millstones and grinding mechanisms
The watermill’s core consisted of paired millstones—the fixed bedstone and the rotating runner stone. The runner stone balanced above the bedstone with a small gap between them and connected to the drive shaft through an iron fitting called a rynd.
Both stones featured complex groove patterns called furrows that spread from the centre. These furrows served three key purposes: they moved ground flour outward, let air pass through to reduce friction heat, and created cutting edges that turned grain into flour. The flat areas between furrows, called lands, did the actual grinding.
The millstones revolved at a steady pace of about 120 rotations per minute.
Millers adjusted the grinding quality through “tentering“—they changed the gap between stones using lever systems. This adjustment determined whether the mill made coarse meal or fine flour, and it required great skill.
Watermills Beyond Flour: Diverse Industrial Applications
Flour milling may have dominated watermill history, but these versatile machines powered many more industries through the centuries. Watermill technology’s adaptability created economic opportunities that reshaped the scene of industrial development in a variety of sectors.
Sawmills and timber processing
Water-powered sawmills became crucial economic drivers in forested regions. Records show sawmills existed in colonial America specifically to process timber, and builders constructed them even before schools or churches. The Garland Brook sawmill in New Hampshire stands as a testament to this technology’s endurance. Built in 1856, it continued to cut red oak logs into lumber using waterpower well into modern times.
These operations typically employed waterpower to drive reciprocating saws. Sawmills appeared along rivers even in areas with limited forest coverage to process valuable walnut and cypress trees that grew near waterways. The United States census of 1840 recorded 31,650 sawmills nationwide.
Textile production and fulling mills
Fulling mills revolutionised textile manufacturing through waterpower. These facilities used huge wooden hammers (fulling stocks) to clean and thicken woollen cloth. The process involved pounding cloth in a mixture of urine and fuller’s earth to create sturdy, windproof material.
France’s earliest documented fulling mill dates to 1086, with another recorded at Temple Guiting, Gloucestershire that same year. The mills’ water-driven fulling hammers worked through a cam mechanism. The waterwheel’s rotation lifted hammers that fell onto carefully folded cloth. Each mill needed about 6 hours to full 6 kilos of cloth.
Metal working and forge hammers
Trip hammers powered by waterwheels changed metalworking capabilities fundamentally. These mechanisms featured a rocker arm attached to a frame, where cams struck tappets to raise massive hammers. La Pianca mill in Italy preserved this system, with separate wooden waterwheels powering each hammer.
Metalworkers used trip hammers for various applications. They drew out iron blooms, shaped wrought iron, fabricated brass, and processed steel. These water-powered hammers first appeared in China during the Western Han dynasty and reached mediaeval Europe by the 12th century.
Paper production
Paper mills needed water both to power operations and as a manufacturing ingredient. Traditional operations used about 17,000 gallons of water to produce one tonne of paper. Modern mills have improved efficiency significantly—some now operate with just 1.5 litres of fresh water per kilogramme of paper.
Paper manufacturers have developed sophisticated water management systems that include closed-loop water treatment to eliminate effluent discharge. Recent technological advances incorporate anaerobic processing that produces biogas, which reduces energy costs and carbon emissions.
Preserving River Watermills as Cultural Heritage
Historic watermills face mounting preservation challenges as their industrial legacy fades. These iconic structures in Britain and Europe are the foundations of our technological and cultural past, which has sparked vital conservation efforts to prevent their deterioration.
Conservation challenges and successes
European conservation programmes work tirelessly to preserve these irreplaceable structures. “Watermills Through the Ages,” 30 years old, provides grants to repair and restore projects in England, Scotland, and Wales. The organisation funds internships and education programmes that teach traditional milling techniques and support research into mill technology. The National Trust’s volunteer engineers and surveyors conduct structural surveys to gather data needed for effective restoration strategies.
Restoration projects thrive on shared approaches. Local associations team up with residents and museum experts to tackle large-scale preservation work. The National Lottery Heritage Fund has helped breathe new life into many forgotten structures, which now serve modern purposes.
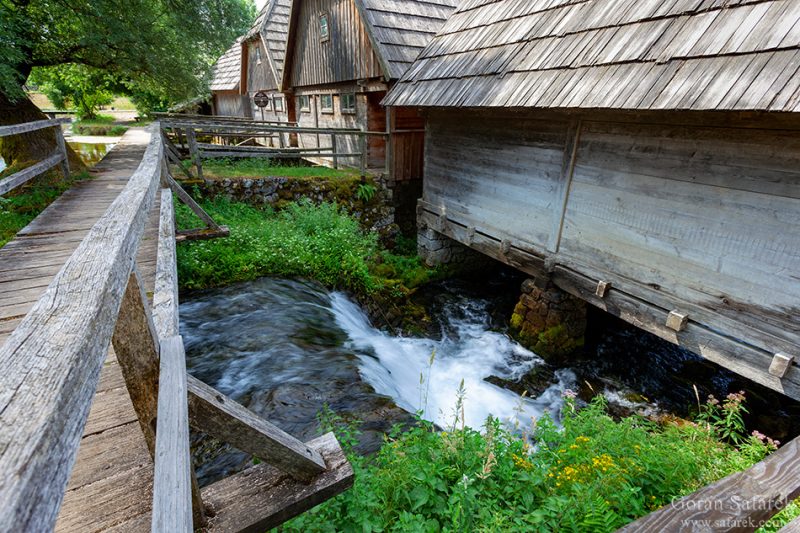
Restored watermills as living museums
Many restored watermills now educate visitors about pre-industrial technologies. Britain’s last working tide mill, Woodbridge Tide Mill, continues its 800-year legacy after recent protection and restoration work. America’s Philipsburg Manor showcases a reconstructed water-powered gristmill that grinds grain and demonstrates 18th-century techniques.
Photo: Martin Pettitt
Maine’s Leonard’s Mills shows how this works perfectly. The site recreates a 1790s logging and milling community on an actual pioneer settlement. Lurgashall Mill takes this concept further – visitors can track flour from the mill and watch bread bake in an eighteenth-century bakehouse’s wood-fired oven.
Modern adaptations of historic structures
Historic watermills now serve new purposes through innovative adaptation. Former mill buildings have become:
- Homes that showcase their industrial heritage
- Businesses ranging from yoga studios to breweries in peaceful rural settings
- Cultural centres that host exhibitions and community events
The 19th-century water mill on Poland’s Molstova River stands out as a prime example. Now known as the “Water Mill Cultural Centre”, this building maintains its historic character while providing valuable community space for arts education and local heritage celebrations.
The Living Legacy of Watermills Today
Though they evoke images of ancient times and pastoral landscapes, watermills are far from obsolete. In fact, across many developing countries, particularly in rural villages and agricultural regions, these humble yet powerful machines continue to serve essential roles in daily life.
In India, watermills—especially the traditional “gharat” used in the Himalayan foothills—are still remarkably common. With over 200,000 units in operation, these mills grind grain, hull paddy, extract oil, and even generate electricity in off-grid mountain communities. In Uttarakhand alone, between 30,000 to 40,000 gharats are currently in use. While many retain their original, hand-crafted wooden components, others have undergone thoughtful modernization—replacing wood with sturdier metal parts to boost both durability and efficiency.
The ingenuity of the Himalayan people has even transformed the gharat into a multipurpose powerhouse, capable of driving several machines at once. This evolution presents a sustainable energy solution for remote hill villages, yet, regrettably, such initiatives have seen little governmental support or promotion.
Nevertheless, these improved watermills are a symbol of resilient, low-cost innovation, combining time-tested design with modern functionality. As cereal grinders, oil expellers, paddy hullers, sawmills, and micro-hydropower generators, they demonstrate how ancient technologies can still meet contemporary needs—especially where large-scale infrastructure is impractical or environmentally unsustainable.
In a world increasingly focused on clean energy and rural empowerment, watermills offer a quiet but potent answer, flowing steadily forward from a rich and ingenious past.
Conclusion
Watermills stand as remarkable proof of human ingenuity, with their legacy spanning over two millennia of technological advancement. Many stopped their industrial operations during the 20th century. These historic structures continue to tell vital stories about technological progress and social development. Their rise from simple grain-grinding mechanisms to sophisticated power systems transformed riverside communities and created the foundation for modern hydroelectric generation.
Historic watermill preservation protects architectural heritage and practical knowledge of eco-friendly power generation. Restored mills serve various purposes now. Some function as living museums, while others have transformed into cultural centres, homes, or businesses. These creative adaptations help these structures survive and maintain their connection to local heritage.
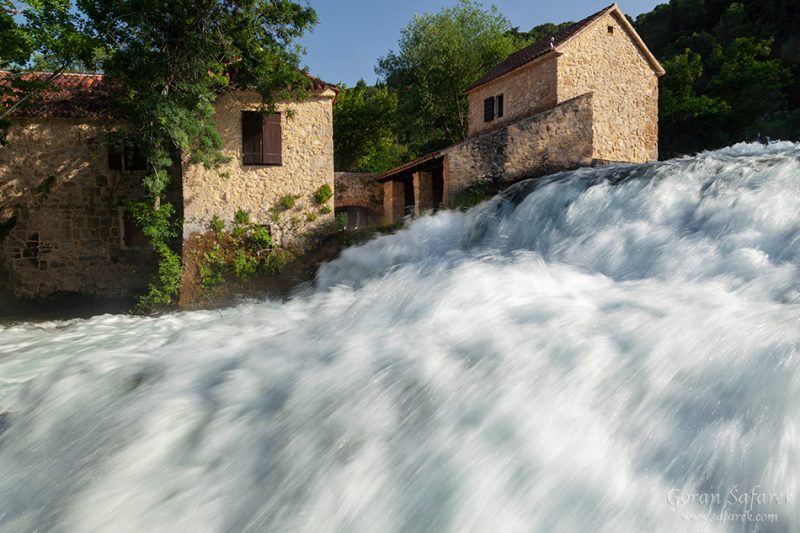
Watermills symbolise more than industrial relics – they represent centuries of engineering achievement and community growth. Future generations will understand and appreciate humanity’s enduring relationship with renewable energy through their preservation. Modern developers can learn valuable lessons about sustainable development from these historical marvels.